Erecting or renovating a steel structure in the modern era typically involves multiple contracted organizations all working together off one set of design drawings. The Engineer, Fabricator, and Contractor hash out design details in a three-way exchange. Using a streamlined structural steel design process can alleviate some of this chaos and the inefficiencies it creates. Furthermore, a streamlined process can lead to significant time and capital savings.
XCEED uses a proven streamlined process to develop advanced fabricator-friendly designs, anticipate difficulties, and cut fabrication and installation costs by 20%.
The Typical Design Process
The Engineer of Record (EoR) creates project design drawings. These drawings convey the EoR’s intent and overall project layout, but typically lack sufficient detail to be used directly by the Fabricator. In some cases, the design of specific details has been delegated to the Contractor. In these cases, it is the responsibility of the Fabricator to create additional drawings combining the EoR’s drawings and the Contractor’s input. Usable erection and shop drawings for each member must be created, submitted, reviewed, and approved by the EoR in a lengthy process. A mountain of documentation that needs to be updated and synchronized can quickly pile up. This is where XCEED’s Streamlined Structural Steel process plays a part.
XCEED’s Proven Process
We use 3D CADD software to build a virtual model, examine site geometry, predict potential problems, solicit stakeholder solutions, and arrive at a more complete design before even a pound of steel is ordered. Once the design is finalized, XCEED creates shop and assembly drawings quickly and efficiently using the refined models. This rapid design process streamlines actual construction, eliminates rework, reduces fabrication and field construction costs and minimizes worker and material waste.
Streamlined Structural Steel – XCEED’s 9 Best Practices
- Availability
- Fabricator Capabilities
- Prefab when Practical
- Shipping and Handling
- Simplicity
- Stability
- Downtime
- Flexibility
- Clearance
Availabillity
Specifying commonly available shapes and grades can help to ensure adequate supplies of raw material. Also check with local and regional Steel suppliers to determine what sort of structural shapes are available in quantity, and at what prices. This can help you choose appropriate members that minimize lead time and cost.
Refer to “Table 2-4 Applicable ASTM Specifications for Various Structural Shapes” of the AISC manual for common material standards.
Fabricator Capabilities
It’s crucial to understand the capabilities of the fabricator; what processes they are capable of and what methods are appropriate for their workflow.
- Which members will be hand-drilled and which will be fabricated by CNC?
- What sort of structural shapes and maximum length members can the fabricator manage?
- What’s the maximum weight they’re able to efficiently handle?
These details are necessary to choose compatible types of steel member, and create suitable shop and assembly drawings. Pre-assembly capabilities are also determined by these factors.
Prefab when Practical
Fabricating items on the construction site, while necessary at times, is a difficult and slow process. Combining these members into ready-to-place assemblies can be even more difficult, depending on the available space. The Fabricator’s workshop is a more ideal assembly environment. However, there are some considerations when determining size and scope of pre-assemblies, most notably shipping and handling.
Shipping and Handling
If there is a will, there is a way. However, possible is not the same as practical or cost-effective. Prefabricating parts and pre-assembling them saves time and money, but make sure members and assembled sections can get from the fabricator to their final installation. Avoid over-sized loads and large pre-assemblies that would be difficult to handle when rigged for placement. Also, make considerations for any pre-existing structures that might block installation or hinder handling, and verify that on-site hoisting equipment can handle the applied loads.
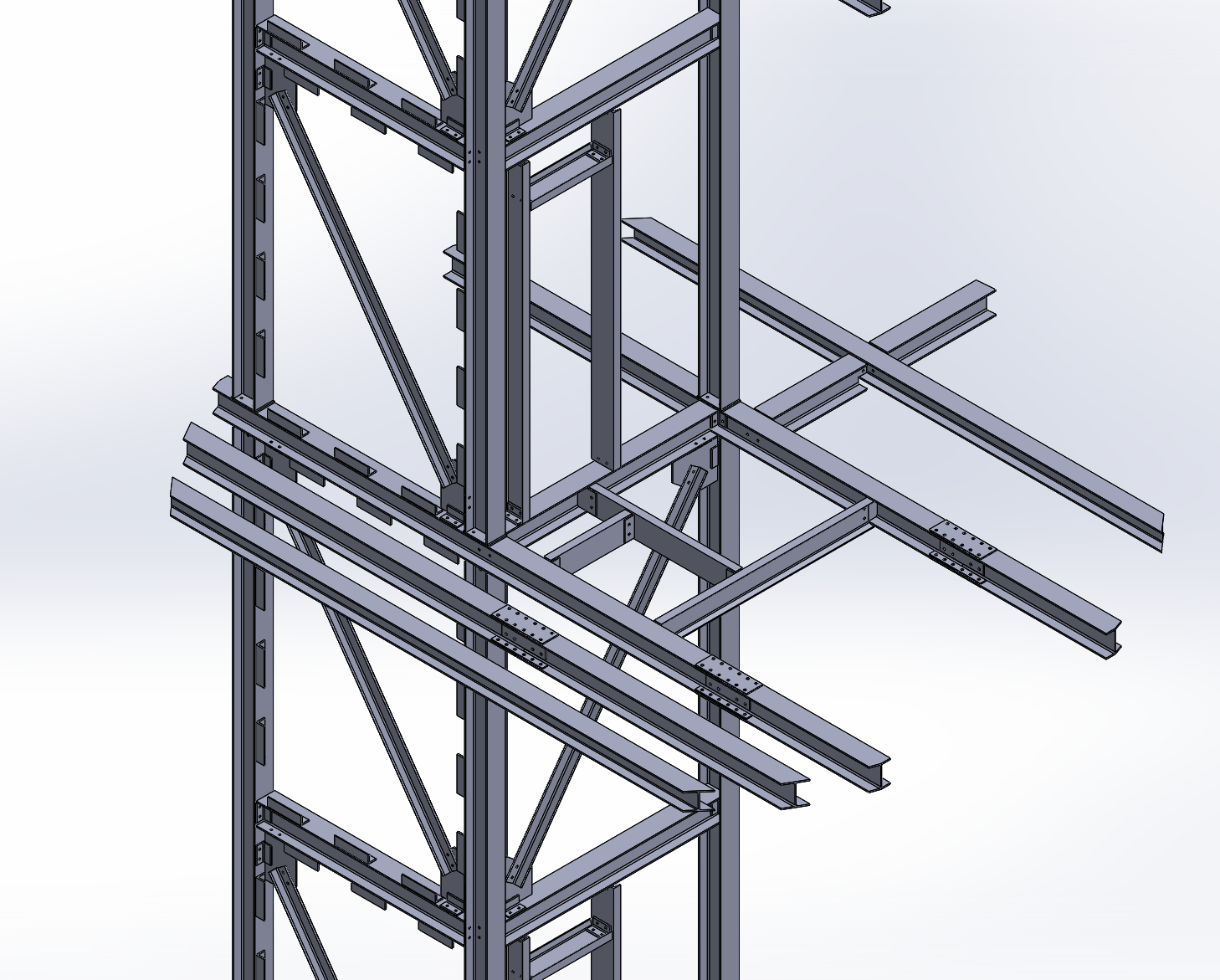
Simplicity
Keep it simple. Simplicity is not only a beautiful thing, but it’s also a good way to save money. Maintaining a consistent bolt size and gage width (adjacent bolt spacing) can minimize errors in fabrication, reduce the number of unique parts, and decrease the likelihood of installation mistakes.
Stability
We provide an installation process that is structurally stable: reduces need for temporary supports and shoring, minimizes installation time, and reduces waste materials. Also, Size bolted connections to be stable using a fraction of the specified bolted fasteners for faster fit-up.
Downtime
Time is money, so it’s best to keep workers moving. Ensure a proper flow of material from the fabricator to keep on-site workers engaged. Specify mechanical anchors over epoxy-based ones to avoid cure-time idleness.
Flexibility
Flexibility is often crucial to achieving a streamlined structural steel process. In our experience, flexibility primarily manifests in two forms: flexibility to operate around existing structures and flexibility to avoid undocumented obstructions (especially when using post-installed anchors).
Existing structures: When accommodating existing structures, provide features that allow for adjustment. To support existing conduit and pipe properly; consider Unistrut, slotted holes, and field drilled holes where appropriate.
Post-Installed Anchors: While necessary, these types of anchors have several inherent difficulties and caveats pertaining to their use. Certain material edge distances must be maintained and concrete masonry wall joints (CMU) avoided. At times, there are pieces of embedded reinforcing steel that interfere with planned anchor placement. This can often be accounted for by providing a slightly larger baseplate size than necessary. When conflicts arise, a larger baseplate permits installers to relocate anchors without the need to rework the structural steel entirely.
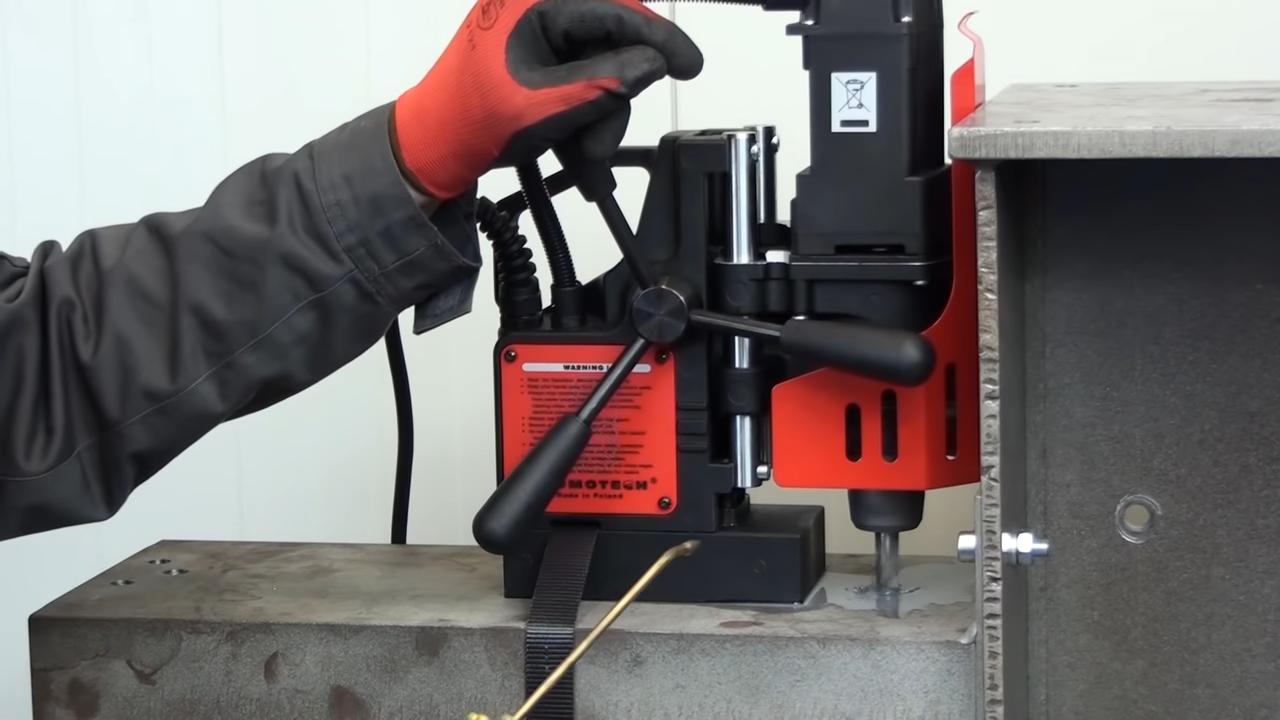
Clearance
It goes without saying; space is a fundamental consideration for any construction project. Keep in mind that there must be tool and worker clearance for any planned field drilling and welding as well. Similarly, spacing out features can simplify the assembly process and avoid costly on-site delays.
Complimentary Consultation With XCEED
Achieving a streamlined structural steel workflow is an intricate and immersive endeavor, but well worth the effort.
Interested in eliminating re-work, accelerating production schedules? How about streamlining structural steel operations and reducing fabrication costs by 20%? Contact XCEED for a complementary consultation today.
Did you find this article helpful? You might also like 5 Tips to Being a Successful Engineer