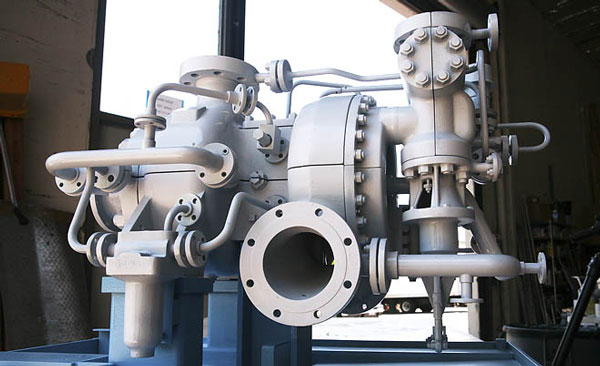
Spare parts management is a complicated, laborious – but critically important – aspect of nuclear plant operation. Ensuring that the right part is available at the right time and the right place requires detailed inventory management, diligent quality control, exacting acceptance testing, etc.
The very fact that spare parts management can be complicated and laborious, however, means that it may be amenable to economic and efficiency improvements. Extra attention in such areas could have big impacts on cost reduction. While several efficiency improvements have been implemented over the years – such as industry-wide databases to locate available replacement parts at nearby plants – a different type of evolving technology could provide the next step change.
Additive manufacturing, 3D printing, flexible manufacturing – whatever term you want to use – is inching its way toward use in the commercial nuclear power industry. I admit that the concept still sounds a bit exotic, and it may take some time to establish compliance with strict material specifications, regulatory and quality assurance requirements, but the prospect of on-demand printing of replacement parts is not that far in the future. In fact, additive manufacturing is already being used to expedite and reduce the cost of certain non-metallic replacement items for nuclear power plants such as electrical connectors.
Moreover, 3D printing is not really that new of a technology. BMW, the German auto maker, has been using 3D printing technologies since the early 1990s, initially for performance race cars, but increasingly for commercial vehicles. The Phantom model, produced by BMW’s Rolls Royce division, now includes more than 10,000 3D-printed components, everything from plastic holders for warning lights to car lock buttons and electronic parking brakes.
BMW cites a number of benefits from 3D printing: faster turnaround times for prototypes; a more efficient production process for complex and high-quality parts; and enhanced quality through tool-less manufacturing. It’s not much of a stretch to translate these benefits to the nuclear power industry, is it? And 3D printing offers another key benefit for the nuclear industry: since parts made for nuclear plants are rarely mass-produced, 3D printing could churn out tailor-made components at lower cost compared with traditional manufacturing methods.
The Department of Energy is funding several projects to investigate the prospects for 3D printing in nuclear power.
At the GE Power Advanced Manufacturing Works facility in Greenville, SC, GE-Hitachi Nuclear Energy (GEH) will use 3D printing to produce mechanical test samples. The samples will then be shipped to the Idaho National Laboratory for irradiation in INL’s Advanced Test Reactor, after which detailed testing will be conducted to compare the irradiated samples with unirradiated samples.
GEH believes 3D printing could reduce manufacturing times by up to a factor of ten, while minimizing waste and enabling low-volume production. Based on the current state of 3D printing technology, initial components will be limited to about 400 cubic millimeters (bread machine size). Potential replacement parts for GEH may include fuel debris filters, control rod drives, and anti-vibration components for jet pumps in boiling water reactors.
“316L stainless steel is our first target alloy,” said Fran Bolger, manager of new product introduction for GE Hitachi Nuclear Energy. “For this material, we already have most of the key data that supports the demonstration of material quality. Some additional data will be generated later this year.”
Depending on regulatory requirements and industry demand, GEH believes parts could be offered to commercial plants as early as 2018. Assuring quality will be paramount. “The metal powder, 3D printing machine and associated build parameters will need to be evaluated for material quality, and the specific printed part build will need to include samples that can be evaluated through nondestructive and destructive testing,” said Bolger. “Some parts may require custom testing critical to the application, such as pressure drop performance.”
Westinghouse is also pursuing 3D printing, leading a second DOE project that will develop and demonstrate a laser-based 3D printing technique for manufacturing metal parts certified for use in nuclear structural applications.
“This is a valuable opportunity for Westinghouse to advance our most innovative nuclear technologies while collaborating across the industry with the best minds in the most advanced research facilities,” said Jim Brennan, Westinghouse senior vice president of the Engineering Center of Excellence.
That last phrase – vitality and economic viability – gets to the heart of it. With all the difficulties swirling about the industry these days, vitality can seem out of reach…a forlorn gaze into the glory days of the nuclear past. However, perhaps 3D printing is part of a technological disruption that will provide a nuclear power industry parallel to the shift from dot-matrix to laser printing: faster, cheaper, at higher quality.
So go ahead. Print that part.
Source: http://www.power-eng.com/articles/print/volume-121/issue-4/departments/nuclear-reactions/print-that-part.html